It is often effective to use copper tubing as single-turn winding on a binocular-core transformer. The tubing has extremely low losses and minimizes leakage inductance which extends the transformer’s high frequency response. Since the companion winding is threaded through the tubing, coupling between the primary and secondary is also very high. In power amplifiers, tubing is often used to minimize losses at high current levels in the low-impedance winding of impedance transformers and combiners. An additional, non-electrical benefit is that soft copper is less likely to scratch a thin layer of enamel on a winding wire.
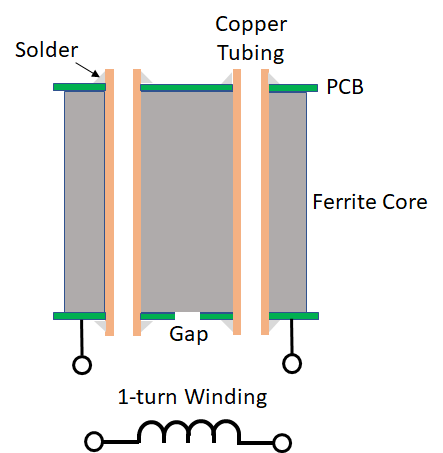
As shown in the drawing, the winding is easiest to make from two straight lengths of tubing with an OD just smaller than the core’s ID. Two pieces of copper-clad PCB are cut and drilled to fit over the tubing and flat against the core. One piece is then soldered to the tubing. This forms the continuous turn on one end of the core.
On the other end of the core, a strip of the copper cladding is removed to form a gap between the tubing pieces so the winding turn is not shorted. The gap is visible in the article’s photograph on page 9 showing SMT resistors connected across the gap. (If double-sided PCB cladding is used, remember to make the gap on both sides of the board!) Each of the now-isolated pads are then soldered to the tubing, and connections to the turn are made to the pads.