In an earlier OnAllBands article (“What Is Ferrite, Anyway?”) I explored the use of ferrite cores for chokes, baluns, and other amateur radio applications. In recent years, ferrite-core components like toroids and beads have become very popular, and they do feature some useful characteristics for use at RF. But what about their older cousins, the powdered-iron components? That’s what we’ll discuss here; the differences in materials and when one type is the better choice.
What is Powdered Iron?
Well, that’s pretty straightforward—it’s iron that’s been ground up into a very fine powder. But what kind of iron? As you might expect, there are different types and different methods of making the powder into cores that have big effects on the core’s performance at different frequencies. This is how Micrometals, a manufacturer of powdered-iron components, describes it:
Powder Core inductor materials are made from discrete particles of ferromagnetic powder. Prior to being formed into a core, the particles are covered in a thin layer of electrically insulated material to ensure electrical isolation of each particle. The particles are then compacted under high pressure to form the core geometry. The electrical insulation between particles enables the materials to be used at high frequency.
The type of ferromagnetic powder that hams use at RF is called carbonyl iron. You may recognize it as a type of dietary supplement, but don’t nosh on a toroid! Carbonyl iron is a highly purified form of iron made from iron pentacarbonyl through a process that uses hydrogen to remove the carbonyl ions, leaving small spherical particles of the purified iron. A carbonyl ion consists of a carbon atom double-bonded to an oxygen atom, so the chemical formula is CO, like carbon monoxide, but with the ability to bond to other atoms, like iron. The particles are coated with insulating material and then formed into cores.
Like ferrite, there are different types of powdered-iron materials called mixes. The size of the iron particles, the type and thickness of the coating, and the process in which the materials are squeezed together all affect the magnetic properties of the mix. Each mix has different properties at different frequencies and power levels.
Comparison to Ferrite
Unlike ferrite, which is made from the metal oxide particles pressed directly together to form a solid ceramic material (a process called sintering), there is no direct contact between the iron particles in a powdered-iron core because of their insulating coating. This means it has a much lower permeability than ferrite. For example, the radio frequency products from Micrometals have permeabilities of 4 to 35, while ferrite mixes used for inductive components range from 125 to 5,000. That means inductance per turn is a lot higher for ferrite.
So you might need fewer turns on a ferrite core, but that isn’t always the best option. The high permeability of ferrite leads to easier core saturation where the material can’t store any more magnetic energy. Saturation means the core has become non-linear, and at RF that creates distortion products. In a receiver’s front-end filters, that overload creates interfering signals. In a transmitter’s output filters or impedance transformers, that creates harmonics and other spurious emissions. The isolation of the iron particles in a powdered-iron core may reduce inductance per turn, but it takes much more energy to saturate. There is also less loss in a powdered-iron core so the “Q”—the ratio of energy lost to energy stored—is much higher. Less loss also leads to lower heating for a given amount of power transferred through the core.
Another significant difference is how the materials respond to temperature changes. Ferrite’s permeability has a much larger variation with temperature, meaning the inductance of a coil or impedance of a choke would change. If the circuit’s performance was not highly dependent on those values, then the change with temperature wouldn’t be a problem. However, if the coil was used in a tuned circuit or precision filter, for example, you would want the least change with temperature. The choice is between cores with high permeability to maximize inductance and cores with good temperature stability.
Selecting a Powdered-Iron Core
In general, if the core will be used in a “narrow-band” circuit (a filter, a tuned transformer, an oscillator, etc.) you should use powdered iron. If the core will be used in an RF transformer that will transfer high power (more than 100 watts, approximately) through the core—called a flux-coupled transformer—then a powdered-iron core will be the usual choice to minimize loss and heating. (In transmitting chokes made of coaxial cable wound on a core—a transmission-line transformer—the power stays in the cable and does not travel through the core. High impedance is the most important thing, so ferrite cores are used here.)
Start by deciding on the mix, making sure the core is intended for use at RF and not as a lower-frequency power conversion material. From the Micrometals website:
-2, -4, -6 & -7 Materials: These are the most popular carbonyl iron mixes. They will provide high Q up to 40 MHz and (are) the most popular for amateur radio and variety of other communication applications. They are also useful for moderate band (width) transformers in the 200 to 400 MHz frequency range.
‐10 & ‐17 Materials: These materials are the highest frequency carbonyl irons. They will provide high Q up to 150 MHz and are a popular material for cable television applications. They will produce moderate band transformers covering 400 to 700 MHz.
Follow the guidelines for whatever circuit you’re building. For example, there are guidelines for how much inductance is required for transformer windings. You’ll have to calculate how many turns are required for that amount of inductance. Choosing the size of the core for transmitting applications is a much more complex process and beyond the scope of this article.
A good guideline is to look at other successful similar designs, then use similar cores. Some trial and error is likely, particularly at high power.
Winding It Up
There are lots of toroid-core circuit designs you can use in the ARRL Handbook, the ARRL Antenna Book, and Experimental Methods in RF Design, the successor to the out-of-print but still popular Solid-State Design for the Radio Amateur. If you plan on doing a lot of building, perhaps purchasing an assortment of cores would be a good investment.
You can see that there are good reasons to have both powdered-iron and ferrite cores in your RF toolbox. If you need a temperature-stable and hard-to-overload core, the powdered-iron versions are your best choice. The basic guidelines for design are available from the manufacturer and in tables such as those in the ARRL Handbook. It’s pretty amazing that we have such a variety of materials to work with as we build our stations!
Editor’s note: Powdered-Iron Cores Now Available at DX Engineering
DX Engineering now carries three sizes of #2 mix powdered-iron core toroids (250 kHz to 10 MHz) in packs of 5, 10, and 25; and two sizes of #6 mix powdered-iron core toroids (3 to 40 MHz) in packs of 25. Look for future OnAllBands posts for more details on DX Engineering powdered-iron cores.
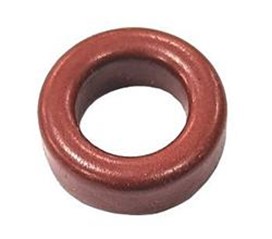
DX Engineering #2 Mix powdered-iron core toroid, 0.500 inch O.D. x 0.303 inch I.D.