Wouldn’t it be great if your antenna system would work forever without any maintenance? Put it up once and enjoy it indefinitely–no tower climbing, cleaning connections, or replacing corroded parts. Maybe if you lived inside a protective dome…
In the real world, there are forces of nature like wind, sun, and rain working constantly to create rust and corrosion, stress metal parts, and destroy electrical connections. If you live near the ocean, you can add salt water to the list. The sea air alone can harm metals since there’s always a small amount of moisture to facilitate corrosion.
Corrosion 101
We’ve all seen corrosion, but what is it exactly? Corrosion is a natural process that converts a refined metal into a more chemically stable form such as an oxide, hydroxide, carbonate or sulfide. It’s the gradual destruction of materials by chemical and/or electrochemical reactions with their environment.
There are three types of corrosion that commonly affect antenna systems:
Galvanic Corrosion occurs when two dissimilar metals are directly or indirectly in contact with each other. It involves an electrochemical reaction caused by the difference in electrode potentials between the two metals. This type of corrosion is identified by the accelerated deterioration of one metal while the other is unaffected.
Pitting is a localized form of corrosion that generally appears as extremely small pits or holes. When in the open air the pits will, in most cases, only reach a small fraction of the metal’s thickness and won’t usually affect the strength of the material.It’s the most common type of corrosion found on aluminum.
Rust is iron oxide formed by a ferrous metal that has been exposed to oxygen and moisture.
Aluminum: One Way to Foil Corrosion
Aluminum is the main material used in most beam and vertical antennas. Why? Because it’s a great combination of the characteristics you need for an antenna. It is more conductive than steel, more corrosion-resistant than copper, and way cheaper than gold.It’s also lightweight and rust-resistant, meaning it doesn’t degrade due to oxidation like steel or other ferrous metals. Rather than flaking through like rust, aluminum oxide forms a hard, whitish-colored surface skin. However, some aluminum alloys are still susceptible to galvanic and pitting corrosion under certain conditions.
Protecting Connections
The basic function of an electrically conductive surface is to permit the flow of electrons in one or more directions. Electrical conductivity of materials can be reduced by corrosion and oxidation, and can interfere with transferring power to the antenna at any point where connections are made. Make sure they are clean, and consider using a good antioxidant joint compound. Sealing the joint makes it airtight, meaning less frequent maintenance.
Better Living Through Chemistry
There are a number of oxide-inhibiting compounds that seal out air and moisture, prevent oxidation or corrosion, survive the elements, and are usable over wide temperature ranges. Some even help conductivity. Here are some examples:
Jet Lube: On bonded metal surfaces, Jet-Lube SS-30 supports electrical and RF conductivity while preventing oxidation and corrosion. The wide temperature range of Jet-Lube SS-30 prevents long-term drying and caking, and allows easy disassembly. Jet-Lube SS-30 is also designed to work as a similar and dissimilar component between two metal surfaces to prevent seizing and galvanic action.
Penetrox A: Antioxidants are electrical joint compounds that ensure a proper electrical connection between aluminum and copper metal parts. Use Penetrox on junctions such as conductors, telescoping aluminum tubing, aluminum to copper connections or other antenna and grounding parts. Penetrox A Antioxidants are compounds of a natural oil base with suspended zinc particles, which ensure high conductivity at all voltage levels by displacing moisture and preventing the corrosion or oxidation of the metal.
Permatex Anti-Seize: Use anti-seize during antenna assembly to prevent galling, galvanic corrosion, and seizing due to weathering or chemicals. Anti-seize assures easier assembly and disassembly of nuts, bolts, and screws.
Loctite Dielectric Grease: This compound may be used in RF connectors to block moisture. Untreated connector threads will oxidize, corrode, and seize more quickly if water vapor can enter and collect inside RF connectors. Feedlines and connectors will last longer with dielectric grease applied. Although the dielectric grease does have insulating properties, contacts are still tight enough to maintain a solid connection–the grease is just displaced.
Kearnalex Connector and Terminal Grease: This product performs the dual function of establishing initial low-resistance contact and permanently protecting the connection by inhibiting corrosion by air, moisture, and other contaminants. Whenever aluminum is involved in an electrical connection, it’s important that the contact surfaces are coveredwith a high-grade corrosion inhibitor and contact aid. Connector and terminal grease can also be used to prevent corrosion and contact degradation with copper and other metals. Kearnalex is available with or without conductive grit.
Joints and Connectors
The compounds listed above are effective. Unfortunately, they won’t last forever and may harden or crack over time. To seal the deal, it’s a good idea to use water-resistant barriers to ensure moisture has no way of creeping into electrical or mechanical connections. This additional step will lessen the need for continued maintenance.
DX Engineering Coax Weatherproofing Kits: The kit has two types of 3/4 inch tape: 3M Temflex™ 2155 Rubber Splicing Tape and 3M Vinyl Electrical Tape for a UV barrier. This combination provides an inexpensive moisture and UV barrier that works for long-term installation, but is also easily and cleanly removed for maintenance.
Scotch Electrical Moisture Sealant Tapes and Pads: Scotch Sealant is an abrasion-resistant sealant roll with an all-weather grade polyvinyl chloride backing that resists moisture, alkalis, acid copper corrosion, and varying weather conditions.
3M Scotchkote FD Electrical Coating: Scotchkote is intended for use as an outer seal on vinyl-tape applications which are subjected to excessive amounts of water or oil. It’s designed to improve the weather resistance of the taped joint or splice. Scotchkote is suitable for direct burial, direct water immersion, or above-ground applications.
Krylon Fusion (clear): Fusion All-In-One provides maximum protection for indoor or outdoor projects without sanding or priming. Recommended surfaces include wood, metal, wicker, plastic, glass, ceramic/plaster, PVC, hard vinyl, tile, wrought iron, masonry, and laminates.
The Galvanic Scale
The galvanic scale (below) ranks a metal’s tendency to react in contact with another metal in the presence of an electrolyte, such as salt water or even moisture from the air. Metals at the top of the chart are called anodic, or active, and are prone to corrode. Metals at the bottom of the list are cathodic, or passive, and rarely corrode.
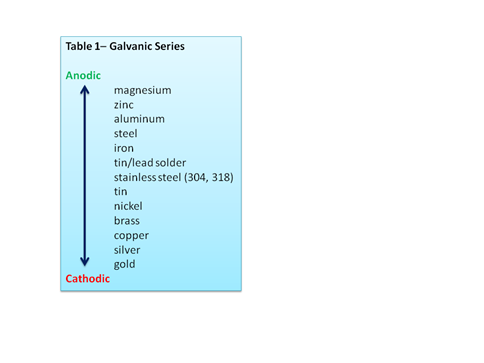
To minimalize corrosion at contact points, use metals that are galvanically similar. Metals close to each other on the scale are usually safe to use together. The further apart two metals are on the chart, the greater their tendency to react and cause corrosion in the more active metal.
One common scenario in antenna installation is connecting a copper feedline to an aluminum antenna part. If you check the chart, copper and aluminum aren’t near each other. However, if you tin the wire with solder or attach a solder lug for the connection, it will probably hold up well. Adding stainless steel hardware to the mix will help maintain a galvanic balance.
Hardware Hacks
Looking again at the galvanic scale, stainless steel is positioned well on the list and has its own anti-corrosion characteristics. Stainless steel is a steel alloy that contains a minimum of 10.5% chromium content. The chromium reacts with the oxygen in the air and forms a protective layer that makes stainless steel highly resistant to corrosion and rust. That’s why many antenna manufacturers choose stainless hardware for their products.
Star washers are another way to discourage corrosion and maintain good electrical conductivity. Under the pressure of the screw and nut holding it, a star washer cuts into the mating surfaces so fresh metal is contacted on both sides. You can get a similar effect by using stainless sheet metal screws driven directly into aluminum parts.
Sandwiching bare copper or tinned copper wire between two stainless flat washers is another solution. It will also lessen the chance of galvanic corrosion.
Doing it Right
Sure, there’s some initial time and expense involved in these extra steps, but they’re worth the effort. Add them to your installation plans and you’ll have reliable, longer lasting connections.